Prototyping is a crucial stage in product development, allowing designers and engineers to transform concepts into tangible objects for testing and evaluation. Among the various methods available for prototyping, 3D printing, and injection molding are two prominent techniques, each with its own set of advantages and limitations. In this article, we will conduct an in-depth comparison of these two methods, aiming to provide a comprehensive understanding of their suitability for different prototyping scenarios.
Exploring 3D Printing for Prototyping
3D printing, also known as additive manufacturing, has gained immense popularity in recent years due to its versatility and accessibility. Here are some critical aspects of 3D printing in the context of prototyping:
Speed and Iteration
3D printing offers rapid turnaround times, allowing designers to produce and iterate on prototypes quickly. Within hours, a digital design can be transformed into a physical object, facilitating a dynamic design process.
Cost-effective for Low Volumes
For small quantities or one-off prototypes, 3D printing is cost-effective. There is no need for expensive molds or tooling, making it an ideal choice for early-stage product development.
Design Freedom
3D printing enables designers to create complex and intricate geometries that would be challenging or impossible to achieve through traditional manufacturing methods. This design freedom fosters innovation and creativity.
Material Variety
3D printers support a wide range of materials, including various plastics, metals, ceramics, and even biodegradable options. This versatility allows for adaptability to diverse project requirements.
Diving into Injection Molding for Prototyping
Although injection molding may not match 3D printing’s speed, its precision and scalability make it a standout in prototyping. The mature manufacturing process excels in producing high-volume, high-quality parts, efficiently utilizing materials, and offering remarkable design accuracy across various production sizes.
High-Quality Reproducible Parts
Injection molding produces parts with exceptional quality and surface finish. This makes it suitable for prototyping scenarios where aesthetics, precision, and functional testing are crucial.
Material Versatility
Injection molding supports a wide array of materials, including thermoplastics, thermosetting plastics, and elastomers. This broad material selection allows for prototypes that closely mimic the final product’s characteristics.
Cost Efficiency for Large Runs
Injection molding becomes cost-effective when producing a large number of parts. Once the molds are created, the per-unit cost decreases significantly, making it an attractive option for mass production.
Durability and Strength
Parts produced through injection molding are often more robust and durable compared to 3D-printed counterparts. This is essential for testing prototypes in real-world conditions.
Comparing 3D Printing and Injection Molding for Prototyping
Let’s conduct a comprehensive comparison of 3D printing and injection molding for prototyping by examining various critical aspects:
- Speed
3D Printing: High-speed for creating prototypes. Ideal for rapid iteration and quick testing.
Injection Molding: Slower setup due to mold creation but efficient for mass production.
- Cost
3D Printing: Cost-effective for small quantities and early-stage prototyping. Minimal setup costs.
Injection Molding: Economical for large production runs but involves higher initial tooling expenses.
- Complexity
3D Printing: Perfect for complex, intricate designs. Offers design freedom.
Injection Molding: Better suited for simpler, standardized designs. Complex molds can be expensive and time-consuming to produce.
- Material Options
3D Printing: There is a comprehensive material variety, but material properties may not match those of injection-molded parts.
Injection Molding: Offers access to a broader selection of materials, including high-performance plastics.
- Quality and Strength
3D Printing: Good quality, but strength and durability may vary by material.
Injection Molding: Produces high-quality, robust prototypes that closely resemble the final product.
- Quantity
3D Printing: Ideal for small quantities, one-offs, or early-stage iterations.
Injection Molding: Cost-efficient for mass production; less practical for small quantities.
- Surface Finish
3D Printing: This may require post-processing for a smoother surface finish.
Injection Molding: Provides excellent surface finish, suitable for prototypes with aesthetic considerations.
Factors Influencing the Choice
Several critical factors should influence your decision when choosing between 3D printing and injection molding for your prototyping needs:
- Project Complexity
The complexity of your design plays a pivotal role. If your prototype demands intricate geometries and rapid iterations, 3D printing offers the flexibility you need. For simpler designs, injection molding may be more efficient.
- Budget
Budget constraints are a crucial consideration. While 3D printing is cost-effective for small quantities, injection molding becomes economical for large production runs. Evaluate your budget to determine which method aligns with your financial limitations.
- Timeline
Project timelines can significantly impact your choice. If time is of the essence, 3D printing’s rapid turnaround is advantageous. Injection molding, while slower to set up initially, can be highly efficient for long-term production.
- Material Properties
Assess the material requirements for your prototype. 3D printing offers a diverse range of materials, but their properties may not precisely match those of injection-molded parts. Injection molding provides access to a broader selection of materials, including those with high-performance characteristics.
- Production Volume
The anticipated production volume is a critical factor. For low-volume runs or one-off prototypes, 3D printing is efficient. In contrast, if you intend to produce a significant quantity of parts, injection molding’s economies of scale come into play.
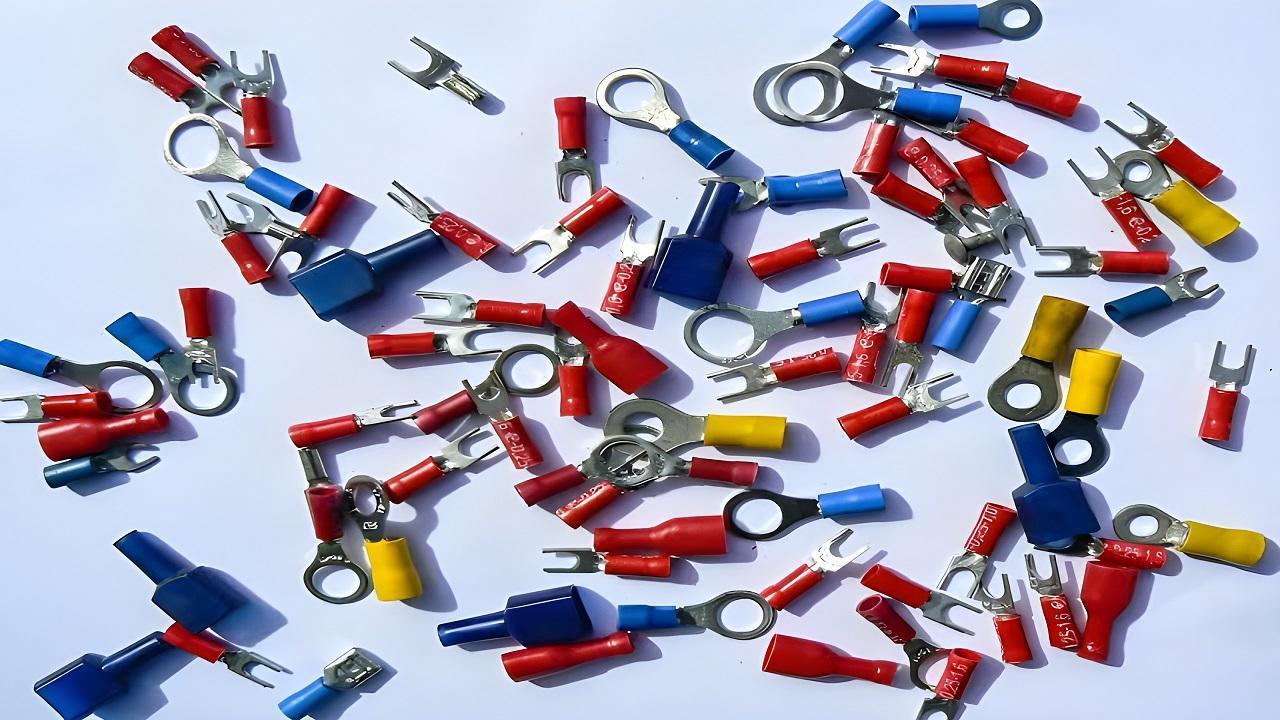
- Surface Finish and Quality
Consider the surface finish and quality required for your prototypes. If aesthetics and precision are paramount, injection molding’s superior surface finish may be more suitable. 3D-printed parts may require post-processing for a smoother appearance.
- Durability and Strength
The expected use of your prototype should guide your choice. If durability and strength are vital for functional testing, injection-molded parts often outperform 3D-printed alternatives.
Conclusion
In the realm of prototyping, both 3D printing and injection molding serve distinct purposes, offering advantages tailored to specific project requirements. The choice between the two methods should be driven by factors such as project timeline, budget constraints, complexity of design, desired material properties, and production volume.
3D printing excels in scenarios demanding rapid iterations, cost-effective small-scale production, and the exploration of intricate designs. Injection molding, on the other hand, shines when high-quality, durable prototypes for mass production are required.
Ultimately, understanding the strengths and limitations of 3D printing and injection molding empowers designers and engineers to make informed decisions that align with their project goals and constraints. The ideal choice depends on the unique needs of the prototyping endeavor at hand.