Firstly, we want to say that casting is actually a manufacturing process where a liquid material is generally powdered into a mold that contains a hollow cavity of the desired shape, and are then allowed to solidify.
And this solidifies part is known as the casting, that is ejected or broken out of the mold to complete the process. Mostly, casting can be of many types i.e. from centrifugal casting, die casting, glass casting to sand casting, slip casting and many more.
What Do You Mean by Sand Casting?
The other name of sand mold casting is sand casting which is actually a metal casting process mainly characterized by using sand as the mold materials. The word “sand casting” also refers to an object produced by using the sand casting process.
During the process of casting, materials present in it are therefore heated to the correct temperature to melt or sometimes treated to modify some of the chemical compositions just to require the desired material properties. Thus almost above 60% of all metal castings are produced by sand casting.
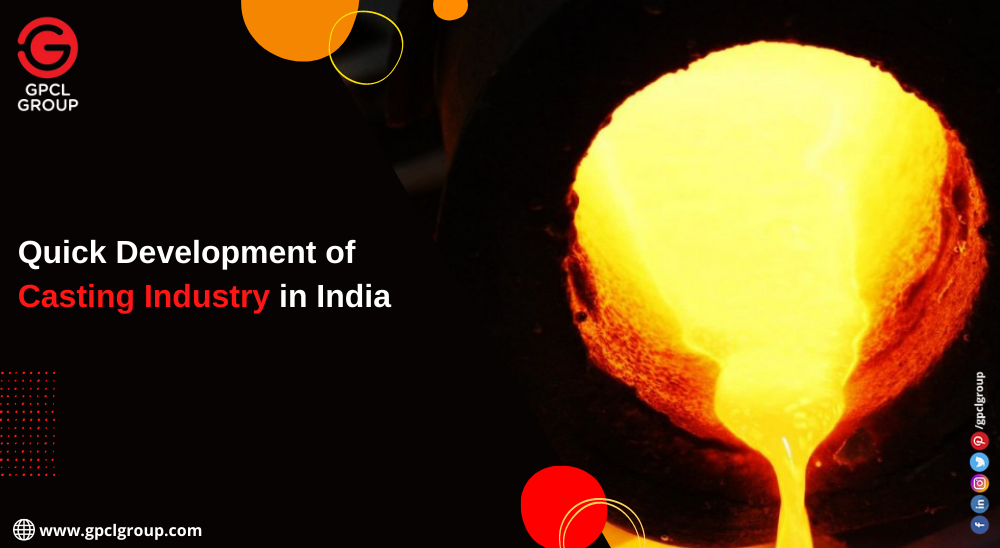
Uses of Sand Casting
Sand casting is mainly used to produce a wide variety of metal components with complex geometries because these parts can, therefore, vary greatly in size and weight, ranging almost from a couple of ounces to several tons.
Other than all these, sand casting is very much common in producing automobile components which include engine blocks, engine manifolds, cylinder heads, and the transmission cases. This how today in India, one will thus find many sand casting manufacturers in India.
Advantages of Sand Casting
- Flexibility in Design
The weight and size of the parts can, therefore, range from few millimeter and grams to meters and many tons. As a result, the size and weight of the cast is limited restrictions imposed by the molten metal supply.
- Provides High Complexity Shapes
For shaping of the complex features, no other range offers the same range of possibilities that can, therefore, be produced near net shape components.
- The Minimum Cost of Tooling
If we compare to other metal manufacturing processes then tooling and equipment costs are very low. This proves that it is one of the cheapest methods to achieve near net shape components.
Disadvantages of Sand Casting:
- Poor Strength Quality
Due to high porosity compared to a machine part, the strength of the material is very low.
- Very Much Low Dimensional Accuracy
The dimensional accuracy is very low because of the surface finish and shrinking.
- Unavoidable Defects
Like most of the other metallurgical processes, defects such as shrinkage, porosity, pouring metal defects, and the surface defects are unavoidable.
As sand casting process is moderately common and even sufficiently refractory for steel foundry use. Therefore, in addition to the sand, a suitable bonding agent is thus mixed with sand.
To make the aggregate suitable for molding, the mixture is moistened typically with water, but sometimes with other components just to increase the plasticity of the clay and to develop the strength.
Therefore, from the first to the current generation we carry out the same motto that, “It doesn’t matter what you want us to make, as long as the consumers are concerned about it.
Read More: