High-frequency pcb, which can be either flexible or stiff, handle operating frequencies of up to 100 GHz and allow quicker signal transmission rates. Materials that are carefully chosen for their low dissipation factor (Df), low dielectric constant (Dk), and limited thermal expansion improve their performance.
High-frequency printed circuit boards, or high frequency pcbare widely utilized in high-density interconnect (HDI) technologies and are crucial parts of radio frequency (RF) microwave and high-speed communications systems. Professional PCB manufacturer Fastlink, with headquarters in China, provides dependable, high-performance a high-frequency PCB fabrication service.
Typically, the frequency range for which we can build high-frequency PCBs is 500MHz to 10GHz. The dissipation factor of high frequency pcb manufacturing is low, usually ranging from 0.0019 to 0.025. Managing the signal transmission rate, reducing signal loss, and improving signal transmission all depend on this low Df.
Enhancing frequency transmission
Lower and steady dielectric constants are essential for effective frequency transmission and decreased signal latency in high-frequency printed circuit boards Enhancing frequency transmission capacities can be achieved with a lower Dk. Because these PCBs are resistant to chemical exposure, they are less likely to corrode or sustain damage in settings where chemical exposure poses a risk.
Due to the low rate of water absorption of the materials used in their production, HF PCBs can withstand humidity without compromising their electrical properties. They retain their shape and size in all-weather situations, hot or cold, due to their limited dimensional stability.
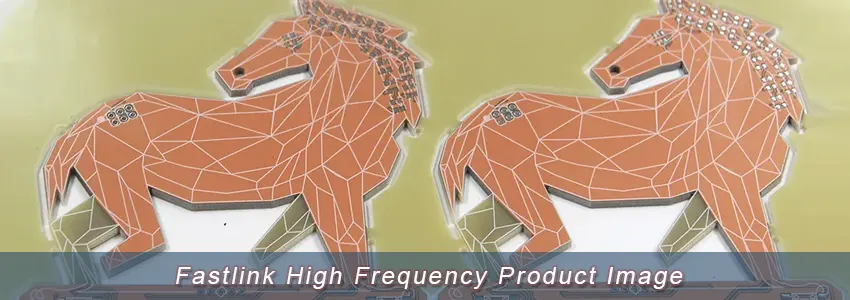
The bulk of high-frequency PCB, often in the range of 0.2–0.3 W/m/K.A thinner substrate could be utilized to reduce the temperature transfer path to the heat sink in order to manage heat more efficiently. However, because of RF heating, a thinner substrate may result in more heat generation.
Specialized substances with low dissipation factor
On the other hand, although a denser substrate with lower insertion loss has a longer heat flow route and can produce less radiofrequency heat, this can be counteracted if the substrate itself has a very low dissipation factor. Teflon and more recent generation substrates are among the materials utilized in HF PCBs; these materials are selected for their low Dk and Df, absorption of water capabilities, and environmental resilience. Although less expensive, materials like FR4 might not function properly at signal speeds higher than 1.6GHz.
High temperature conductivity and low loss are claimed by some laminates. The RT/Duroid 6035HTC, for example, has a very high thermal conductivity of 1.44 W/m/K and a very low dissipation factor. For high-frequency, high-power PCB applications, choosing the appropriate material is essential to ensuring effective thermal management. Specialized substances with low dissipation factor (Df) and dielectric constant (Dk) are used to make HF PCBs.
Df measures the amount of energy lost as heat, while Dk measures how much a substance slow down an electrical transmission. At high frequencies, low Dk and Df reduce attenuation and distortion of the signal. For high-frequency performance, the traces’ geometrythe conductive routes on the PCBis essential. Carefully regulating trace widths and spacing is necessary to reduce signal distortions and interference..